Top 10 Largest Cement Manufacturers, Suppliers & Exporters In India
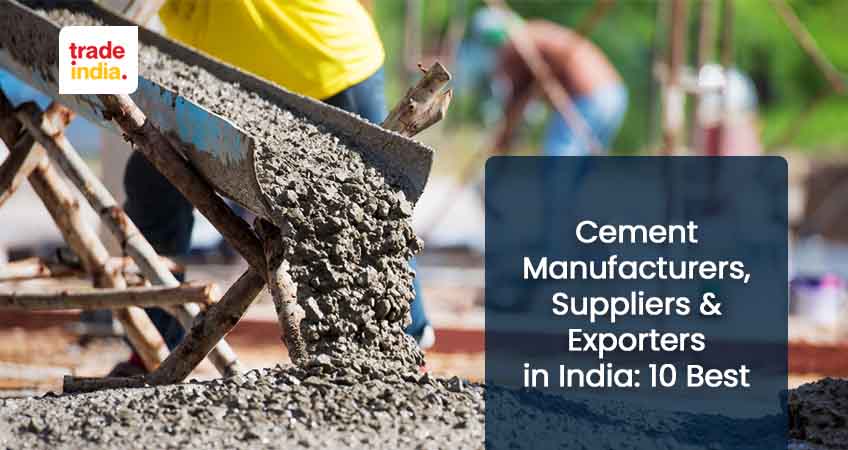
In building, cement is a particularly effective binding substance. Cement has become an essential civil engineering material due to its numerous uses in various building disciplines. It's utilized to build key engineering buildings, including “bridges, culverts, dams, tunnels, and lighthouses”, among other things. Cement is also used as a concrete admixture, which proves to be a basic material for any form of construction, including “schools, housing, hospitals, roads, dams, and ports”, as well as for decorative purposes (for “floors, staircases, patios, driveways, and pool decks”) and items such as sculptures, tables, and bookcases.
Cement industry in India:
A Kolkata-based corporation was founded in 1889. The business became more structured in the early nineteenth century, and it is now the world's second-largest cement production after China. Throughout 2019, the South Asian country produced over 340 million metric tonnes of cement. There are around 450 small and big cement factories in the industry.
Demand and supply:
The housing industry generated the most demand inside the country, accounting for more than 60% of total demand in 2017. The government established an Affordable Homes Fund under the "National Housing Bank", which assisted residents in obtaining financing to purchase homes, resulting in increasing demand. With almost one million metric tonnes of anticipated exports, Sri Lanka was the leading destination for cement kiln exports outside the country in 2016.
Creating something together:
Companies began forming joint ventures to address rising domestic and international demands. In 2017, there were 14 mergers and acquisitions within the cement and construction industry. Cement is a precious product because of its composition possibilities and function as a binder. India is the world's second-largest cement manufacturer, accounting for more than 7% of worldwide installed capacity. In FY22, India's total cement manufacturing capacity was over 545 million tonnes (MT). The private sector owns 98 percent of the total capacity, while the state sector owns the balance. The top 20 businesses produce around 70% of India's total cement production. Because India has abundant and high-quality limestone reserves throughout the nation, the cement sector has enormous expansion potential.
Because of the rising demand in many sectors, including housing, commercial building, and industrial construction, cement demand is predicted to reach 419.92 MTPA by FY 27.
In February 2021, India's cement output grew by 7.8% over February 2020.
In FY21, India's total cement output was 262 million tonnes (MT) (Till February 2021).
According to ICRA, cement output in India is predicted to expand by 12% YoY in FY22, owing to increased demand for rural homes and the government's clear emphasis on infrastructure investment.
According to Crisil Ratings, the Indian cement sector is expected to add 80 million tonnes (MT) output by FY24, the most in ten years, due to rising expenditure on housing and infrastructure.
Also Read: How To Start A Cement Bricks Manufacturing Business in India - 2023 Guide
Cement manufacturing process:-
Here Is The Complete Updated List of Top 10 Most Popular Cement Manufacturers in India:-
1:- UltraTech Cement Ltd
In India, it is the leading producer of grey cement, ready-mix concrete (RMC), and white cement. It has become one of the world's major cement manufacturers. Ultratech is the biggest of India's top five cement businesses. As part of the Aditya Birla Group, Grasim Industries owns Ultra-Tech.
2:- Ambuja Cements Ltd.
LafargeHolcim, a global firm, is among the ten top cement companies in India. It is currently the second cement manufacturer in terms of revenue. Ambuja Cement has been providing hassle-free home-building solutions since its foundation, thanks to its specialized sustainable development efforts and ecologically friendly practices. Ambuja Cement is among the top five cement companies in India.
3:- ACC Ltd.
With 17 cement manufacturing plants, 75 ready-mix concrete facilities, over 6,700 people, a massive distribution structure of 50,000+ distributors and retailers, and a national spread of sales offices, it is one of India's most giant cement and readily available concrete producers. It is India's third-largest cement producer and is one of the best cement companies in India.
4:- Shree Cement Ltd.
In terms of revenue, it ranks fourth amongst the top ten cement companies. The famed Bangur family of Kolkata founded the company in 1979. In 1985, the first cement plant was built, with a throughput of 0.6 Mtpa. The company's total cement capacity is now 29.30 million tonnes.
5:- Dalmia Bharat Ltd
Is ranked fifth among some of the top ten cement companies in total revenue. The company operates a cement production factory with a capacity of 9 million tonnes per year in the southern regions of Tamil Nadu (Dalmiapuram & Ariyalur) and Andhra (Kadapa).
6:- Birla Corporation Limited
The M.P. Birla Group's flagship company Mr. Madhav Prasad Birla, who founded the Birla Jute Manufacturing Company Limited in 1919, was the one who gave it shape. He turned the company from a jute products maker to a major multi-product firm with diverse operations as Chairperson.
7:- India Cements Ltd
Sri T S Narayanaswami and Sri S N N Sankaralinga Iyer formed the organization in 1946. They possessed the foresight to inspire hopes for an industrialized India, the capacity to turn those ideas into reality, and the ability to forge lasting connections and a bright future.
8:- The Ramco Cements Limited
The Ramco Group's leading firm is a South Indian corporate conglomerate. Chennai is the company's headquarters. Being one of the best cement manufacturers, it ranks eighth among India's top ten cement businesses. The company's main product is Portland cement, which is produced in eight cutting-edge production facilities, including the Integrated Cement Factory and Grinding Units, with a capacity of 16.45 MTPA.
9:- Orient Cement Ltd
Orient Cement was founded in 1979 as an Orient Paper & Industries division. It was founded in 2012 and has become one of India's extraordinarily fast-growing and leading cement makers.
10:- Heidelberg Cement India Ltd
Through the brownfield development of its plants in Central India in 2013, the Company raised its production to 5.4 million tonnes per annum. It is ranked 10th among the top cement companies in India.
Conclusion
By 2025, India's cement capacity will reach 550 MT. The cement industry is predicted to reach 550-600 million metric tonnes (MTPA) by 2025, increasing diverse sectors such as healthcare, commercial development, and industrial construction.
FAQs: Cement manufacturers
Q. What is the dry cement process?
Ans. Crushed raw materials are fed into something like a grinding mill in precise quantities in both dry and semi-dry cement production processes. In the grinding mill, the raw ingredients are dehydrated and reduced to a fine powder.
Q. What is the use of limestone in cement?
Ans. The limestone functions as a crystal for the cement, dispersing reaction products more evenly and enhancing the cement's reactivity.