Top 10 Grinding Machine Manufacturers, Suppliers, and Dealers in India
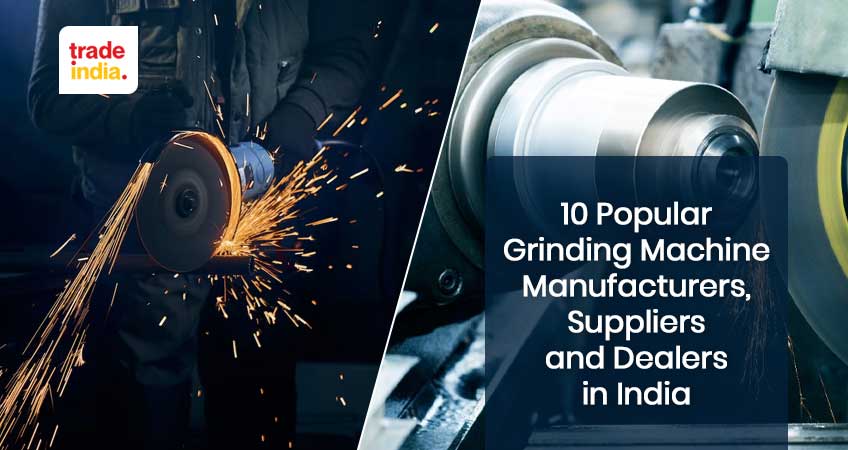
The dynamic world of manufacturing has its unsung heroes at work: Industrial Grinding Machines. With unmatched potential, exceptional power, and precision, these machines have been shaping the future of manufacturing and production sectors. Whether it is metal, wood, or other substances, they play an important role in shaping and finishing various materials by removing excess material. These indispensable tools that shape our everyday products optimise the production processes, elevate quality standards, and reduce costs.
Benefits of Industrial Grinding Machines
These machines ensure improved efficiency and precision with their high-speed material removal properties. From grinding large components to small, intricate workpieces, they can handle a wide range of materials and sizes. With automated processes, these machines are sure to reduce labour costs, enhance productivity, and minimise material waste.
To boost the working speed and output of the processes, manufacturing units should buy high-end industrial grinding machines from leading brands. In this blog, the Top 10 Grinding Machine Manufacturers, Suppliers, and Dealers in India are listed to help you choose the best for meeting your production demands:
Micromatic Grinding Technologies Ltd.
Established in 1973, Micromatic Grinding Technologies Pvt. Ltd. (MGT) has been offering technically sound grinders in CNC, PLC, and Hydraulic versions. With three plants in Ghaziabad near New Delhi, the company has emerged as the market leader with a 50% market share in India.
Jyoti CNC Automation Ltd.
Jyoti CNC Automation Limited is one of the biggest grinding machine manufacturers offering computerised machine cutting tools. The company has three different plants at Metoda, GIDC, and Rajkot, Gujarat, with a manufacturing capacity of 3000 machines annually. It has a strong sales network across Argentina, Austria, Australia, Portugal, Russia, Slovakia, South Africa, Turkey, Azerbaijan, Bangladesh, Sri Lanka, Spain, Switzerland, Tunisia, Belarus, France, Germany, Great Britain, Brazil, China, the Czech Republic, Hungary, Italy, the Middle East, the Netherlands, and the USA.
Ace Micromatic Group
The Group has more than five decades of rich expertise and experience in running eight principal companies. With an installed base of more than 55,000 machines across the world, it has become one of the major grinding and milling machine Suppliers in India. It has more than 500 members and modern production units located over an area of 50000 square metres in Bangalore, India, to design state-of-the art technology, machines, and tools.
United Grinding Group
It is one of the world’s leading grinding machine manufacturers, with 20 manufacturing units, service centres, and sales locations. It offers a wide range of brands such as MGERLE, BLOHM, JUNG, STUDER, etc. for the production of high-precision components.
BFW (Bharat Fritz Werner) Limited
Bharat Fritz Werner Ltd. (BFW) is one of India's leading grinding machine dealers, established in the year 1961 in collaboration with Fritz Werner Werkzeugmaschinen GmbH, Germany. It is operational in 15 countries through channel partners and service centres in 48 locations across the country. With five technology centres and two state-of-the-art manufacturing plants, the company has been continuously offering ground-breaking solutions.
HMT Machine Tools Limited
The company was founded in 1953 to offer a wide array of heavy-duty grinding machine and tools to the manufacturing sector. Six manufacturing units spread across the country with a team of experienced engineers have been helping the company create value-added solutions with innovative technologies.
Aatomize Manufacturing Private Limited
The company was incepted in 2010 as a prominent manufacturer and trader of high-end grinding machines. It is an ISO 9001:2008 certified company that produces more than 20,000 machines per month. With two high-tech production units, it has been developing exceptional machines to satisfy the needs of the market. The grinding machine price is very low, ensuring that it caters to the demands of every size business, from small to large.
Jones & Shipman Hardinge Ltd.
This is one of the principal grinding machine manufacturers, offering matchless solutions for every need. It offers advanced, high-precision solutions with over 125 years of experience. The company has been catering to the demands of customers and partners in over 65 countries.
Wendt India Limited
With innovative business strategies, a vast product portfolio, and strong product development, the company has been serving more than 750 direct customers in the market. It was incorporated in 1980 as a Joint Venture between Wendt GmbH and The House of Khataus.
Prayosha Enterprise
The company provides unmatched grinding solutions to the markets of Uganda, Bahrain, Oman, South Africa, Kenya, Algeria, Qatar, the UAE, and the global market. Located in Gujarat, India, it has been delivering excellence with unmatched production skills and vast expertise in the domain of grinding.
FAQs: Grinding machine
Q. What is a grinding machine, and what is its purpose?
Ans. A grinding machine is a mechanical device designed with abrasive wheels or belts to remove material from a workpiece. It is ideal to shape, finish, and refine surfaces by removing excess material and achieving precise specifications in manufacturing and production processes across various industries. The prime purposes of grinding machines include:
Surface finishing
Material removal
Tool sharpening and reconditioning
Achieving precise dimensions and tolerances
High-volume production
Q. What are the different types of grinding machines available?
Ans. Surface Grinding Machines: They produce a smooth and flat surface with their back-and-forth movement across the workpiece. They can be operated manually or with CNC controls for accurate and repeatable surface finishes.
Cylindrical Grinding Machines: They are perfect for grinding the outer surfaces of cylindrical workpieces with their rotating grinding wheels.
Centerless Grinding Machines: In these machines, the workpiece is supported by the regulating wheel, grinding wheel, and work blade for high-volume production.
Bench Grinders: Bench grinders are small grinding machines mounted on a bench or pedestal. They are used for general-purpose grinding tasks, such as sharpening tools, shaping metal objects, etc., in workshops and tool rooms.
Internal Grinding Machines: These machines are used to grind the internal surfaces of cylindrical workpieces with small grinding wheels that rotate inside the workpiece. They are one of the best options for grinding bores and holes in bearings and cylinders.
Tool and Cutter Grinding Machines: Tool and cutter grinding machines are widely used to sharpen and recondition different cutting tools like drills, milling cutters, and tool bits.
Jig Grinding Machines: These advanced machines are extensively utilised for grinding complex shapes and creating holes in workpieces with a precision grinding head guided by a jig or template.
Gear Grinding Machines: These high-tech machines are specifically designed for the grinding of gears and gear-related components. They are excellent options for producing high-precision gears with matchless surface finishes.
Q. How does a grinding machine work?
Ans. A grinding machine is designed with a workpiece of metal or wood. This is fixed to the machine's worktable or chuck. One or more grinding wheels rotate at high speeds. You can change the position and depth of the grinding wheel to get the desired material removal and surface finishing. When grinding wheels come into contact with the workpiece and apply pressure to the surface, the material is removed using cutting, shearing, and rubbing actions. This process is continued until the desired surface finish, dimensions, or tolerances are achieved. You can also get machines with coolant to reduce the chances of heating and damaging.
Q. What are the common applications of grinding machines?
Ans. Manufacturing and Metalworking Industries: Grinding machines are widely used in removing excess material, refining surfaces, and achieving precise dimensions. They are used in metal fabrication, automotive, aerospace, machinery, and other sectors for surface grinding, cylindrical grinding, tool and cutter grinding, and centerless grinding.
Automotive Industry: These machines are used for engine component finishing, brake rotor surfacing, and gear manufacturing.
Medical Industry: They are used in the production of surgical instruments, orthopaedic implants, and dental tools in medical sector.
Bearing Manufacturing: Grinding machines are used in the bearing manufacturing industry to attain precise dimensions and surface finishing.
Tool and Die Making: For tool sharpening, reconditioning, and surface grinding of the cutting tools, these machines are used for prolonged tool life.
Woodworking Industry: In the woodworking industry, they are used for sharpening and shaping cutting tools, smoothing surfaces, and making wooden components for assembly.
Precision Machining: They are used for grinding precision parts, moulds, and dies with tight tolerances and complex geometries.
Q. Can grinding machines be used for both rough and finished grinding?
Ans. Yes, grinding machines are used for both rough and finished grinding.
Rough Grinding: Rough grinding is the first stage of the grinding process, where large amounts of material are removed quickly. Coarse grinding wheels or abrasive belts are used for rough grinding and achieving a fine surface finish. This process is crucial for removing surface defects, shaping the workpiece, and preparing it for subsequent finishing operations.
Finish Grinding: Finish grinding is the final stage of the grinding process that produces a smooth, accurate, and quality surface finish. Small amounts of material are used for eliminating remaining imperfections, refining dimensions, and improving the overall surface texture.
EXPLORE MORE: