Top 11 Types of Prefabricated Structures - [2025]
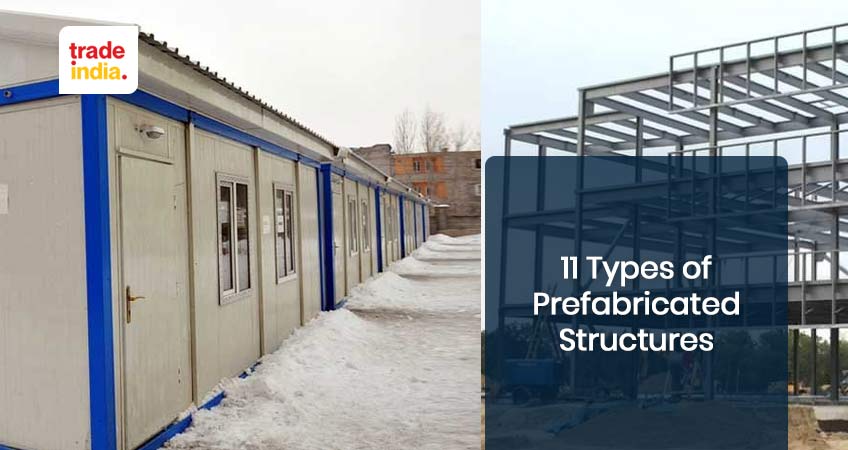
A prefabricated structure is a building or sub - assemblies that has been constructed or erected in whole or in considerable part employing closed construction away from the actual construction site.
Because of the greater precision afforded by a factory setting, prefabrication can save time and money compared to traditional on-site building methods. Walls, ceilings, and floors tend to recur in most structures, which makes it easy to sequence together a set of actions that can be used in production. The production process can be optimised by studying and enhancing these procedures.
Many examples of prefabricated buildings can be traced back to nomadic times, when people were constantly moving to explore new places. Modular homes and temporary settlements became essential throughout the colonisation era. Once the colony was established, however, there was no longer a pressing demand for prefabricated buildings.
Producing items on a prefabricated structure production line allows for a quicker turnaround time, which is one of the key advantages of this method of production. Employees are more productive than those on a standard building site because they follow well-defined routines when carrying out their responsibilities.
Top Prefabricated Structures Types
1. Temporary Prefabricated Structures
Whether you need a structure for interior or outdoor use, a prefab building can meet your needs. They are manufactured in a panel fashion, with a steel or aluminium framework and a covering. Many materials, such as fibreglass, glass, and polyvinyl chloride, can be used to construct shelter walls (PVC). Temporary shelters that are prefabricated are easy to set up and install.
They are long lasting and need no upkeep, and can resist even the most extreme climate conditions like as high heat and low cold and humidity. Prefabricated shelters have several practical use outside providing shelter for humans, including housing for rescue gear, soundproofing for pumps, and covering for audio gear in recording studios.
Prefabricated shelters are versatile because they may be modified to fit a wide range of uses. Because of how quickly they can be put together and put into action, they are perfect for use in times of crisis.
2. Fiberglass Prefabricated Structures
Prefab structures often use fiberglass since it is both inexpensive and long-lasting. Because of its well sealed structure, it is resistant to the growth of mold and rust and may be used for outdoor constructions without fear of harm from water or the accumulation of moisture. Its resilience to wind, heat, and cold makes fiberglass an ideal material for use in the wall cladding of prefabricated buildings.
Fiberglass may be shaped and molded into a wide variety of forms, and it can be colored to match any aesthetic. Fiberglass prefabricated houses are strong and long-lasting because the plastic composite foundation material is flexible and resistant to tensile stress.
3. Quonset Huts
Because of its dome shape, Quonset huts, which are composed of steel alloys, are also known as arch steel buildings. Quonset huts are among the most popular prefab options since they are cheap, require little upkeep, and can resist natural disasters like earthquakes.
Quonset huts, with its time-tested design, have served as homes for many cultures over the years. The modern Quonset hut has all the benefits and designs of the original Quonset hut, plus the addition of cutting-edge engineering and construction methods.
They are produced in two-foot-wide parts, making it simple to modify the design to fit a variety of needs. Quonset huts owe their basic structure to the arch, which allows for both structural support and a spacious, unobstructed interior.
4. Hybrid Prefab Systems
Modular and panel systems' three-dimensional and two-dimensional components are combined in hybrid prefab systems to form either an entire structure or an individual section of one.
These prefabricated steel structure share characteristics with both panel systems and modular. Modular modules have the upper hand in terms of build quality and attention to detail, but they have drawbacks when it comes to assembly and shipping.
5. Structural Insulated Panels
The SIP is a sandwich panel used as a concrete building's structural member (e.g., for the roof, walls, and floors). It typically consists of two skinned, progressively thicker layers of hard material surrounding a more flexible core.
A wide range of materials can be used for it depending on its function. It is often constructed from polyurethane or another plastic foam (PUR). When it comes to resistance to fire, smoke, and flame, PUR foam is unrivaled.
6. Ferrocement Sandwich Panel
Buildings in developed countries often make use of ferrocement, a type of laminated building material. Silos, chemises, infill frames, walls, water tanks, and maritime structures are only few of the many applications.
Ferrocement is made up of sand, wire mesh, cement, and water, and it has several desirable features including being antirust, fire-resistant, seismic, and hurricane-proof. It is also utilized for fixing broken structures or retrofitting older ones.
7. Wafflecrete Building System
The large structural ribbed panels connected with reinforced precast concrete are used to construct building that welded together and the joints between both the modules are caulked to create the walls, pitched, floors, and flat roofs. Each panel's surface is made up of a slab that is 51 mm thick, and the prefabricated structure manufacturers panels themselves are either 152 mm or 203 mm thick.
Prefabrication reinforced concrete floor panels anchored by precast concrete grade joists on well-compacted ground are used to create the floors of single-story buildings.
8. Open Sided Modules
Each of the module's one or two sides is made to open completely. If you want to make a bigger room by connecting open-sided modules together, you'll want to get rid of the long sides first. Gusset plates and bracings connect the corner posts to the edge beams, which bear the weight of the structure.
Tall buildings can't be made out of open-sided modules due to a lack of sufficient load-bearing elements. This style of architecture is often two or three floors high. Both healthcare facilities and educational institutions could benefit from these programs.
9. Modules Supported
A steel structural frame is placed to the outside of this sort of module to help with load bearing and transfer. Because the modules are piled overhead, the exterior construction can give open spaces on ground level or below.
Moreover, it can provide complete module support while allowing the walls and dividers to be non-load bearing. In most cases, this kind of construction is used for dwellings or mixed-use retail and residential structures.
10. Insulated Precast Concrete Panels
Insulated precast concrete panels are built in a similar way to structural insulated panels (SIPs), with two structural facings binding an insulating material. The wythes, or concrete strata, that serve as the facings in this style.
More robust structural performance can be attained by pre-stressing these wythes. The insulation is a proprietary stiff substance. The three parts are rigid and can carry weight on their own, making them versatile in how they're assembled or broken down. The wythes can either be rigidly connected or allow some degree of movement or deflection.
Because of their solid connections, fully composite panels may withstand greater loads than their less reinforced counterparts. Connectors made from non-composite materials can move or bend and are resistant to stress but vulnerable to shear.
11. Insulated Concrete Forms
For the purpose of constructing sturdy concrete walls, this panel employs hard insulating elements as permanent formworks. On-site assembly of the formworks, ties, and other structural components. They can be fabricated as separate modules that fit snugly with one another to create a structure. A long-lasting barrier is constructed by pouring ready-mix concrete at the spot.
After that, you can apply the finish or cladding system right to the prefabricated structure insulation. The building wasn't entirely prefabricated, although a lot of the work was done in a factory.
As the primary load-bearing structure, ICFs often perform better than alternative panels. They are more durable and impervious to water damage because of their one-piece structure.
A roof, Walls, and a floor all make up prefabs, shorthand for buildings that are constructed in a factory. Some or all of these parts can be put together in a factory before being shipped to the construction site.
Prefab structures have different categories depending on how much they are built. Component, panel, module, hybrid, and full buildings are all distinct types of construction.
FAQs: Prefabricated Structures
Q. What are prefabricated structures?
Ans. Prefabrication is a method of mass-producing construction components in advance of their eventual assembly on-site. Prefabricated structures have their individual parts or modules manufactured in a factory and then sent to the construction site for final assembly.
Q. How does the cost of prefabricated structures?
Ans. The cost of the prefabricated Structure is between Rs 17,000 to Rs 95, 0000 in India.
Q. What types of materials can be used for prefabricated structures?
Ans. Steel, concrete, and wood are the common type of materials used for prefabricated structures.
Q. What are 3 advantages for using prefabrication?
Ans. Here are the top 3 advantages of using prefabrication:
- Environment friendly
- Durable
- Quality Control Construction
Related Blog Topics: