What Makes Titanium Such a Difficult Material to Machine?
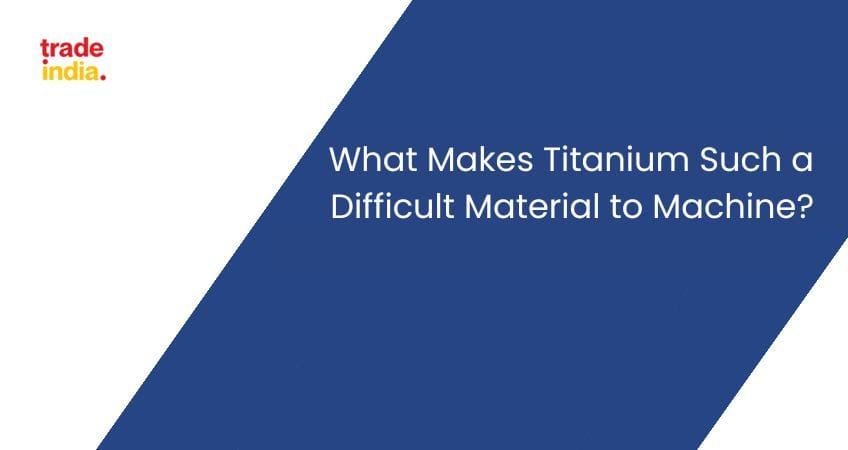
Introduction
Metal titanium (chemical symbol Ti) is the tenth most common element on Earth. However, trace amounts of titanium can be discovered in nearly every type of rock, despite its rarity in substantial deposits. Titanium, a silvery-gray metal with a low corrosion rate and excellent strength, has many practical uses.
Titanium makes up 0.44 percent of the crust of the Earth and is found everywhere across the planet. Titanium in the crust of the Earth is almost exclusively found in ilmenite minerals (90–95%). The chemical formula for ilmenite is FeTiO3, which stands for "iron titanium oxide," the compound of iron, titanium, and oxygen.
Titanium's +4 oxidation state predominates in titanium chemistry because it is the element's most stable oxidation state. In contrast, titanium compounds in the +3 oxidation state are frequently encountered. In general, complexes of titanium have an octahedral coordination geometry, with TiCl4 being the only notable exception.
Why is Titanium Such a Difficult Material to Machine?
1. Physical phenomena in titanium processing
Titanium alloys have a somewhat stronger cutting force than steel of the same hardness; however, the physical phenomenon of processing titanium alloys is significantly more complex than that of steel processing, resulting in significant challenges.
Most titanium alloys only have a heat conductivity of 1/7 that of iron and 1/16 that of aluminum. As a result, the heat generated during the cutting of titanium alloy is not dissipated into the workpiece or removed by the chips, but instead is concentrated in the cutting area, where it can reach temperatures of 1000 °C or higher. This causes the cutting edge of the tool to wear, crack, and produce chip tumors quickly, and the rapid appearance of a worn cutting edge causes the cutting area to generate even more heat.
The cutting process generates a lot of heat, which degrades the surface integrity of titanium alloy parts, which in turn causes a drop in geometric precision and the work hardening phenomena, which significantly lowers fatigue strength.
Although titanium alloy's elasticity may improve component performance, it significantly contributes to vibration during cutting due to elastic deformation of the workpiece. Because the "elastic" workpiece leaves the tool and bounces back under the cutting pressure, the friction between the tool and the workpiece cancels out the cutting effect. The frictional process also generates heat, exacerbating the issue of titanium alloy's low thermal conductivity.
2. Titanium alloy is notoriously tricky to work with, and "heat" is the real "culprit" here
Processing technology used by titanium manufacturers highlights for titanium alloys
The primary knowledge of processing titanium alloy is as follows, based on an understanding of the processing mechanism of titanium alloy and prior experience:
- Cutting force, heat generated during cutting, and deformation of the workpiece can all be minimized by employing a blade with positive-angle geometry.
- If you don't want the workpiece to harden, keep feeding it. At all times during the cutting process, the tool should be in the feeding state. At least 30% of the radius must be removed (the AE).
- To keep the machining process from overheating, which could lead to surface degeneration or tool damage, a high-pressure, high-flow cutting fluid is used.
- Heat and wear on the blade edge can quickly cause the instrument to break, therefore it's important to maintain its sharpness.
- Titanium alloy is easiest to work within its softest form, as it becomes more challenging to shape after hardening. However, heat treatment increases material strength and blade wear.
- When cutting through hard materials use a big tip radius or chamfer and if possible, use multiple blades. This can mitigate localized damage by lowering the cutting force and temperature at each site. When milling titanium alloy, the radial cut (milling depth) AE and cutting speed are the two most important factors in determining tool life VC.
3. Starting from blade to solve the problem of titanium processing
In titanium alloy machining, the blade's groove wear is the back-and-forth local wear along the cutting depth direction, and it's usually produced by the hardening layer left over from the last operation.
An additional factor in the development of groove wear is the chemical reaction and diffusion of cutting workpiece and tool material at processing temperatures above 800 °C.
As the titanium molecules of the workpiece build up in front of the blade, they "weld" to the blade under the intense heat and pressure of the machining process, creating a tumor called chip accretion. The blade's cemented carbide coating is lost when the chip accumulation is peeled off.
Therefore, titanium alloys processing calls for a unique blade material and geometry.
Also, Read - Metals & Alloys Manufacturers, Suppliers & Exporters in India - Top 10
4. Tool structure matches for titanium Machining
When working with titanium alloys, heat is where the action is. It is important to spray the cutting edge with a lot of high-pressure cutting fluid at the right moment and in the right place so that the heat can be dissipated as soon as possible. For milling titanium price alloys, there is a milling cutter on the market with a particularly designed structure.
5. Tooling for cutting Titanium
Ti can be both sticky and hard, making it difficult to select tooling. Cutter blades with fewer flutes are the norm when working with sticky materials. In contrast, when milling tough materials (such as stainless), a cutter with many flutes is preferable to provide adequate engagement at the necessary feed rates.
In order to overcome the wear and heat problems that titanium inevitably causes, positive cutting geometries on the cutting tools are highly recommended. A tool nose radius or cutters with rounded inserts can achieve this.
6. Coolant
When trying to maintain a comfortable temperature, coolant is essential. Cutting titanium causes it to heat up, thus applying coolant directly to the blade can be quite helpful. Ti is notoriously sticky, therefore removing the resulting chips is essential for clean cutting.
7. Cutting Titanium when it is soft
Take advantage of titanium's hardening properties by heating it. Several forms of Ti are commercially available. A more manageable method involves first finding the alloy's weakest state and then using heat to harden it.
8. Titanium Solution
Machining titanium and its alloys present unique challenges, but the methods for addressing them are quite stable. Galling, heat generation, work hardening, and workpiece or tool deflection are four major issues that must be avoided. Keep the tool in motion when it is in contact with the workpiece, use a slow and steady feed rate, apply a lot of coolant at high pressure, and utilize as stiff a setup as feasible.
In addition, picking the right coating for your tools is crucial to the outcome of your work. Having a coating that can appropriately deal with the heat generated during titanium uses is crucial for preserving performance throughout an operation.
How To Machine Titanium Work?
Coated carbide tools, which can withstand the alloy's stickiness and break up lengthy chips, are necessary for machining titanium. The coating on the tools makes it easier to control the heat generated during machining.
To reduce heat production and the inclination toward work hardening, radial engagement must be kept low. End mills with more flutes can boost output despite the decreased feed per tooth.
High-pressure coolant application is used to lessen the heat and wear on the tool. Right now, work is being done on perfecting ultrasonic-assisted machining. Time spent in touch with the tool is minimized in order to increase its service life.
Machining titanium color with the right method can also yield better results. Titanium can be machined with less tool damage and better results by employing techniques such as employing a secondary relief tool design, "climb milling," arcing in, adjusting the axial depth, ending on a 45-degree chamfer, and utilizing a tool that is at least 70% smaller than the tool pocket.
Conclusion
You may optimize your tool and your final product by learning about titanium's peculiarities and then altering your machining processes accordingly. The skilled experts can help you create a titanium solution tailored to your needs with further machining assistance. Machine cutters will be in more demand as the use of titanium and its many alloys spread across more and more sectors. In contrast, a successful run can be achieved with the right coating, heat management, and chip evacuation.
FAQs: Titanium
Q. Is titanium dangerous to people?
Ans: Titanium is not toxic, and it is safe for human consumption even in huge quantities. The toxicity of titanium and titanium dioxide is quite low. Lung disorders such pleural disease can be triggered by titanium exposure, along with chest pain, tightness, trouble breathing, coughing, and skin/eye irritation.
Q. What are titanium's flaws?
Ans: Above 400 degrees Celsius, its strength begins to degrade, therefore it's not ideal for use in high-temperature applications; instead, use a nickel-based superalloy that can withstand extreme heat. While machining, it is crucial to make use of the appropriate cutting tools, as well as the appropriate speeds and feeds.
Q. Is it easy for titanium to rust?
Ans: Rust and corrosion don't seem to bother it as much as they do other metals and alloys. Titanium's highly active connection with oxygen allows it to withstand sea water for a century without corroding.
Q. Does a magnet stick to titanium?
Ans: Titanium, being a paramagnetic substance, does not interact with the MRI's magnetic field in any way.
Related Blogs: